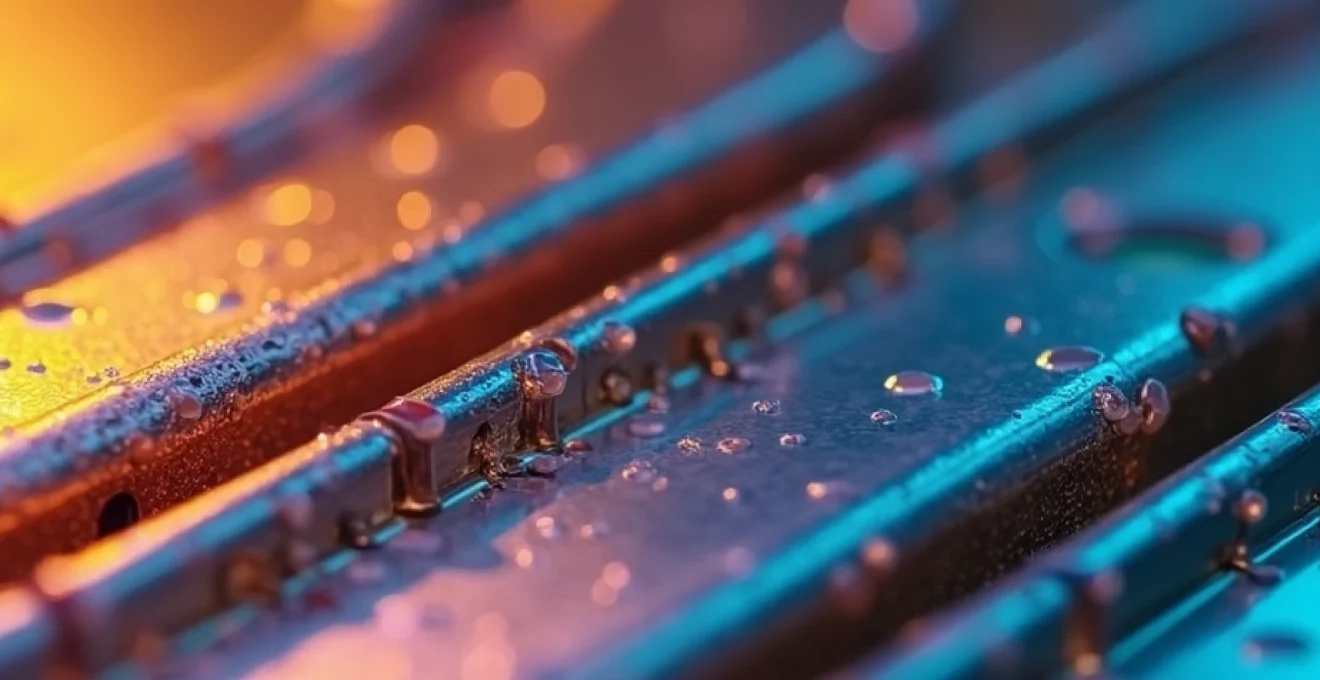
L'aluminium anodisé est un matériau aux multiples facettes, offrant une combinaison unique de durabilité, d'esthétique et de polyvalence. Ce procédé de traitement de surface transforme l'aluminium ordinaire en un produit aux propriétés remarquables, ouvrant la voie à une multitude d'applications dans divers secteurs industriels. De l'aérospatiale à l'architecture, en passant par l'électronique grand public, l'aluminium anodisé joue un rôle crucial dans notre vie quotidienne, souvent sans que nous en ayons conscience.
Procédé d'anodisation de l'aluminium
L'anodisation est un processus électrochimique complexe qui modifie profondément les caractéristiques de surface de l'aluminium. Cette technique, développée il y a près d'un siècle, continue d'évoluer et de s'améliorer grâce aux avancées technologiques et à la recherche constante d'optimisation.
Bain électrolytique et formation de la couche d'oxyde
Le cœur du procédé d'anodisation réside dans l'immersion de l'aluminium dans un bain électrolytique. Généralement, on utilise une solution d'acide sulfurique comme électrolyte. Lorsqu'un courant électrique traverse le bain, une réaction d'oxydation se produit à la surface de l'aluminium, qui agit comme l'anode du système. Cette réaction entraîne la formation d'une couche d'oxyde d'aluminium (Al2O3) extrêmement dure et poreuse.
La structure poreuse de la couche d'oxyde est particulièrement intéressante. Elle se compose de millions de minuscules pores hexagonaux, disposés de manière ordonnée perpendiculairement à la surface du métal. Cette configuration unique permet non seulement d'augmenter considérablement la surface totale de la pièce, mais offre également des possibilités fascinantes en termes de coloration et de fonctionnalisation ultérieure.
Paramètres clés : densité de courant, température et durée
La qualité et les propriétés de la couche anodisée dépendent de plusieurs paramètres critiques qui doivent être soigneusement contrôlés tout au long du processus. Parmi ces paramètres, trois se distinguent par leur importance capitale :
- La densité de courant : elle influence directement la vitesse de formation de la couche d'oxyde et sa structure.
- La température du bain : elle affecte la porosité et la dureté de la couche anodisée.
- La durée du traitement : elle détermine l'épaisseur finale de la couche d'oxyde.
La maîtrise précise de ces paramètres permet aux ingénieurs de tailor les propriétés de la couche anodisée en fonction des exigences spécifiques de l'application visée. Par exemple, une anodisation à basse température et haute densité de courant produira une couche plus dure et plus résistante à l'usure, idéale pour des applications mécaniques exigeantes.
Types d'anodisation : sulfurique, chromique et dure
Il existe plusieurs types d'anodisation, chacun présentant des caractéristiques uniques adaptées à des besoins spécifiques :
- Anodisation sulfurique : C'est la méthode la plus courante, utilisant l'acide sulfurique comme électrolyte. Elle offre un bon équilibre entre coût, durabilité et possibilités de coloration.
- Anodisation chromique : Utilisant l'acide chromique, cette méthode produit une couche plus fine mais offre une excellente résistance à la corrosion. Elle est particulièrement appréciée dans l'industrie aérospatiale.
- Anodisation dure : Réalisée à basse température et haute densité de courant, elle crée une couche extrêmement dure et résistante à l'usure, idéale pour les applications mécaniques exigeantes.
Le choix du type d'anodisation dépend des propriétés recherchées et de l'application finale du produit. Par exemple, l'anodisation dure pourrait être privilégiée pour des pièces soumises à des frottements intenses, tandis que l'anodisation chromique serait préférée pour des composants aéronautiques exposés à des environnements corrosifs.
Propriétés et applications de l'aluminium anodisé
L'aluminium anodisé se distingue par un ensemble de propriétés remarquables qui en font un matériau de choix dans de nombreux domaines. Ces caractéristiques uniques ouvrent la voie à des applications innovantes et à des solutions techniques avancées.
Résistance accrue à la corrosion et à l'usure
L'une des propriétés les plus appréciées de l'aluminium anodisé est sa résistance exceptionnelle à la corrosion. La couche d'oxyde formée lors de l'anodisation agit comme une barrière protectrice, isolant le métal sous-jacent des agents corrosifs de l'environnement. Cette protection est particulièrement précieuse dans les applications maritimes ou industrielles où les matériaux sont exposés à des conditions agressives.
En outre, la dureté de la couche anodisée, qui peut atteindre 9 sur l'échelle de Mohs (le diamant étant à 10), confère à l'aluminium une résistance à l'usure exceptionnelle. Cette propriété est exploitée dans la fabrication de composants mécaniques soumis à des frottements intenses, comme les pistons de moteurs ou les engrenages.
Isolation électrique et conductivité thermique modifiée
La couche d'oxyde formée par anodisation possède des propriétés diélectriques intéressantes. Elle agit comme un isolant électrique, permettant l'utilisation de l'aluminium anodisé dans des applications électroniques sensibles. Cette caractéristique est particulièrement utile dans la conception de boîtiers pour appareils électroniques, où l'isolation électrique est cruciale pour éviter les interférences.
Paradoxalement, bien que la couche d'oxyde soit un isolant électrique, elle n'affecte que marginalement la conductivité thermique de l'aluminium. Cette propriété est exploitée dans la conception de dissipateurs thermiques pour l'électronique de puissance, où l'aluminium anodisé offre un excellent compromis entre isolation électrique et dissipation thermique.
Utilisation dans l'aérospatiale : alliages 2024-T3 et 7075-T6
L'industrie aérospatiale est l'un des plus grands consommateurs d'aluminium anodisé, en raison de ses propriétés uniques de légèreté et de résistance. Deux alliages en particulier sont largement utilisés dans ce secteur :
- L'alliage 2024-T3 : Connu pour sa résistance à la fatigue, il est couramment utilisé dans la fabrication de fuselages d'avions.
- L'alliage 7075-T6 : Offrant une résistance mécanique exceptionnelle, il est privilégié pour les structures portantes comme les ailes.
Ces alliages, une fois anodisés, offrent une combinaison optimale de légèreté, de résistance mécanique et de résistance à la corrosion, essentielle pour les applications aérospatiales. L'anodisation chromique est souvent préférée dans ce domaine en raison de sa capacité à former une couche protectrice fine mais très efficace contre la corrosion.
Applications architecturales : profilés schüco et systèmes technal
Dans le domaine de l'architecture et du bâtiment, l'aluminium anodisé est plébiscité pour sa durabilité, son esthétique et sa facilité d'entretien. Deux acteurs majeurs se distinguent dans ce secteur :
Schüco , entreprise allemande leader dans les systèmes de fenêtres, portes et façades, utilise extensivement l'aluminium anodisé dans ses profilés. Ces profilés allient légèreté, résistance aux intempéries et esthétique moderne, répondant ainsi aux exigences les plus strictes des architectes contemporains.
De son côté, Technal , fabricant français de systèmes architecturaux en aluminium, propose une gamme de produits anodisés qui se distinguent par leur design innovant et leurs performances thermiques. Les systèmes Technal sont particulièrement appréciés pour leur capacité à combiner efficacité énergétique et esthétique raffinée.
L'aluminium anodisé a révolutionné l'architecture moderne, offrant aux concepteurs un matériau à la fois durable, esthétique et performant sur le plan environnemental.
Ces applications architecturales illustrent parfaitement la polyvalence de l'aluminium anodisé, capable de répondre aux défis techniques tout en satisfaisant les exigences esthétiques les plus pointues.
Coloration et finition de l'aluminium anodisé
La coloration de l'aluminium anodisé ouvre un vaste champ de possibilités esthétiques, permettant d'adapter le matériau à une multitude d'applications décoratives et fonctionnelles. Les techniques de coloration ont considérablement évolué, offrant aujourd'hui une palette de teintes et d'effets visuels presque illimitée.
Procédé électrolytique intégral (EII) pour teintes métalliques
Le procédé électrolytique intégral (EII) est une technique avancée permettant d'obtenir des teintes métalliques d'une grande stabilité. Cette méthode consiste à déposer des particules métalliques directement dans les pores de la couche anodisée, créant ainsi une coloration intégrée à la structure même du matériau.
L'EII permet d'obtenir une gamme de teintes allant du bronze clair au noir profond, en passant par des nuances de champagne et d'or. Ces teintes métalliques sont particulièrement appréciées dans l'architecture haut de gamme et le design industriel, où elles apportent une touche de sophistication et de modernité.
Coloration par absorption de pigments organiques
La coloration par absorption de pigments organiques est une méthode plus traditionnelle mais toujours largement utilisée. Elle consiste à immerger l'aluminium anodisé dans un bain de colorant, permettant aux pigments de pénétrer dans les pores de la couche d'oxyde.
Cette technique offre une palette de couleurs extrêmement vaste, allant des teintes pastel aux couleurs vives et saturées. Elle est particulièrement appréciée dans les applications décoratives et le design de produits grand public, où la variété des couleurs est un atout majeur.
Technique de coloration interférentielle pour effets irisés
La coloration interférentielle est une technique innovante qui exploite les propriétés optiques de la couche anodisée pour créer des effets visuels fascinants. Elle repose sur le dépôt de couches nanométriques de matériaux transparents dans les pores de l'oxyde, créant des interférences lumineuses qui produisent des effets irisés changeants selon l'angle de vue.
Cette technique permet d'obtenir des finitions uniques, avec des effets de couleurs changeantes et des reflets métalliques subtils. Elle trouve des applications dans le design haut de gamme, l'industrie automobile et l'architecture contemporaine, où elle apporte une dimension esthétique inédite.
La coloration de l'aluminium anodisé ne se limite pas à l'esthétique ; elle peut également améliorer certaines propriétés fonctionnelles du matériau, comme l'absorption ou la réflexion thermique.
La maîtrise de ces différentes techniques de coloration permet aux concepteurs de créer des produits en aluminium anodisé qui allient performance technique et esthétique raffinée, répondant ainsi aux exigences les plus élevées en termes de design et de fonctionnalité.
Normes et contrôle qualité de l'anodisation
La qualité et la performance de l'aluminium anodisé dépendent fortement du respect de normes strictes et de procédures de contrôle rigoureuses. L'industrie a développé un ensemble de standards et de certifications pour garantir la conformité des produits anodisés aux exigences les plus élevées.
Norme ISO 7599 pour les spécifications générales
La norme ISO 7599 est la référence internationale pour les spécifications générales de l'anodisation de l'aluminium et de ses alliages. Elle définit les exigences techniques pour les différents types d'anodisation, y compris les épaisseurs minimales de couche, les tolérances dimensionnelles et les méthodes de test.
Cette norme couvre également les aspects liés à la préparation de surface, aux conditions de traitement et aux procédures de contrôle qualité. Elle est essentielle pour assurer la cohérence et la fiabilité des produits anodisés dans différents secteurs industriels.
Label qualanod pour l'anodisation architecturale
Le label Qualanod est une certification spécifique pour l'anodisation architecturale, reconnue internationalement. Ce label garantit que les produits anodisés répondent aux normes les plus strictes en termes de qualité, de durabilité et de performance environnementale.
Pour obtenir la certification Qualanod, les fabricants doivent se soumettre à des audits réguliers et des tests rigoureux. Le label couvre différents aspects de la production, incluant :
- La qualité de la couche anodique
- La résistance à la corrosion
- La solidité de la coloration
- L'uniformité de l'aspect visuel
Le label Qualanod est particulièrement important dans le secteur du bâtiment, où la durabilité et l'esthétique des composants en aluminium anodisé sont cruciales.
Tests de résistance : brouillard salin et abrasion taber
Pour éval
uer la résistance et la durabilité des revêtements anodisés, l'industrie utilise plusieurs méthodes de test standardisées. Deux des plus importantes sont le test au brouillard salin et le test d'abrasion Taber :
Le test au brouillard salin simule un environnement marin ou industriel agressif. Les échantillons anodisés sont exposés à une brume saline pendant une période prolongée, généralement 1000 heures ou plus. Ce test évalue la résistance à la corrosion du revêtement anodisé et sa capacité à protéger le métal sous-jacent dans des conditions extrêmes.
Le test d'abrasion Taber, quant à lui, mesure la résistance à l'usure de la couche anodisée. Il utilise des roues abrasives qui tournent sur la surface de l'échantillon, simulant une usure mécanique intense. La perte de masse ou le changement d'apparence après un nombre défini de cycles permet de quantifier la résistance à l'abrasion du revêtement.
Ces tests rigoureux permettent non seulement de valider la qualité des produits anodisés, mais aussi d'orienter la recherche et le développement vers des revêtements toujours plus performants.
Innovations et tendances en anodisation
Le domaine de l'anodisation de l'aluminium est en constante évolution, porté par les avancées technologiques et les nouvelles exigences en matière de performance et de durabilité. Plusieurs innovations récentes ouvrent de nouvelles perspectives pour ce procédé centenaire.
Anodisation plasma électrolytique (APE) pour revêtements céramiques
L'anodisation plasma électrolytique (APE) représente une avancée significative dans le domaine des traitements de surface de l'aluminium. Cette technique utilise des tensions électriques élevées pour créer des micro-décharges plasma à la surface du métal, résultant en la formation d'un revêtement céramique extrêmement dur et résistant.
Les revêtements APE offrent une résistance à l'usure et à la corrosion supérieure à celle des anodisations conventionnelles. Ils trouvent des applications dans des domaines exigeants tels que l'industrie automobile (pour les pistons et les cylindres de moteurs) et l'aérospatiale (pour les composants soumis à des contraintes thermiques et mécaniques élevées).
Nano-anodisation et structures auto-organisées
La nano-anodisation est une technique émergente qui permet de créer des structures nanométriques hautement ordonnées à la surface de l'aluminium. En contrôlant précisément les paramètres d'anodisation, il est possible de produire des réseaux de nanopores ou de nanotubes avec des dimensions et des configurations spécifiques.
Ces structures nano-anodisées ouvrent la voie à de nombreuses applications innovantes, notamment :
- Des surfaces super-hydrophobes pour l'auto-nettoyage
- Des substrats pour la croissance de cellules en ingénierie tissulaire
- Des électrodes à haute surface spécifique pour le stockage d'énergie
La capacité à contrôler la morphologie à l'échelle nanométrique offre des possibilités fascinantes pour adapter les propriétés de surface de l'aluminium à des applications spécifiques.
Anodisation verte : électrolytes sans chrome et économies d'énergie
Face aux préoccupations environnementales croissantes, l'industrie de l'anodisation s'oriente vers des pratiques plus durables. Deux axes majeurs se dégagent dans cette quête d'une anodisation plus verte :
1. Le développement d'électrolytes sans chrome : L'anodisation chromique, bien que très efficace, utilise du chrome hexavalent, un composé toxique et cancérigène. Des recherches intensives sont menées pour trouver des alternatives plus écologiques, comme les électrolytes à base de sulfate-borate ou de phosphate-permanganate, qui offrent des performances comparables sans les risques environnementaux.
2. L'optimisation énergétique du processus : L'anodisation est un procédé énergivore. Des efforts sont déployés pour réduire la consommation d'énergie, notamment par l'utilisation de systèmes de refroidissement plus efficaces, l'optimisation des paramètres de traitement, et le développement de procédés à basse température.
L'avenir de l'anodisation se dessine à travers ces innovations, alliant performance, durabilité et respect de l'environnement. Comment ces avancées transformeront-elles l'industrie dans les années à venir ?
Ces développements récents illustrent la vitalité du domaine de l'anodisation de l'aluminium. En combinant des techniques avancées comme l'APE et la nano-anodisation avec une approche plus respectueuse de l'environnement, l'industrie se prépare à relever les défis futurs en matière de performance des matériaux et de durabilité.